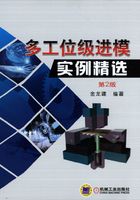
2.11 连接板多工位级进模
1.工艺分析
图2-44为某电子产品的连接板。其材料为SUS430(不锈钢),料厚0.4mm,年产量100多万件。该制件结构简单,在生产中需经过冲裁、翻孔、弯曲等工序组合而成。经合理分解后,按一定的成形顺序设置在不同的冲压工位上。
图2-44 连接板
从图2-44中可以看出,制件的弯曲内R较小(接近为零),因此弯曲时对板料纤维方向有一定的要求,若纤维方向同弯曲线平行,制件在弯曲之后会出现开裂、断裂现象,影响使用质量。若采用单工序模,生产效率低,制件精度无法保证,不能满足生产需求,故选用多工位级进模生产。
2.排样设计
制件展开图见图2-45。该制件有毛刺方向的要求,需向下弯曲成形才能达成。计算出弯曲展开长度为59mm,宽度为15.8mm。
该制件裁料方式为直裁,使弯曲线与板材纤维方向垂直,这样能很好控制弯曲件的开裂、断裂问题。为了提高材料利用率,各工位间排列紧凑,步距为17mm,采用单排排列、双侧载体的排样方式。
带料以两侧直边为导向送料,设置冲切侧刃为粗定距,两侧的φ3mm导正销孔为精定距。制件排样图见图2-46。具体工位安排如下:
工位①:冲导正销孔及冲切侧刃。
工位②:压字印。
工位③:预冲孔。
工位④:翻孔。
工位⑤:冲切废料。
工位⑥:空工位。
工位⑦:冲切中部废料。
工位⑧:空工位。
工位⑨:“U”形弯曲。
工位⑩:空工位。
工位(11):切断(制件与载体分离)。
图2-45 制件展开图
图2-46 排样图
3.模具结构设计
连接板多工位级进模结构如图2-47所示。该模具设计要点如下:
(1)模具结构
1)该模具采用滚动式自动送料机构,传送各工位之间的冲裁及弯曲成形等工作;用内、外导料板导料、套式顶料杆及顶块抬料;利用切断凹模将已成形好的制件从带料上切断,使分离后的制件左侧尾部下装有轻微的浮料块向上顶,使制件沿着下模板的斜坡滑下。
2)凸模、凹模等各零件采用SKDII,热处理硬度为60~62HRC;固定板、卸料板、下模板采用Cr12MoV,热处理硬度为55~58HRC;固定垫板、卸料板垫板及下模垫板采用Cr12钢,热处理硬度为53~55HRC。凸模与固定板的配合间隙单面为0.005mm;凸模与卸料板之间的配合间隙单面为0.0075mm;导正销与卸料板的配合间隙单面为0.005mm;凹模镶件与凹模板为零对零配合;顶杆、套式顶料杆与凹模板之间的配合间隙单面为0.01mm。
图2-47 连接板多工位级进模结构
1—上模座 2—卸料板 3—固定板垫板 4、8、10、14—卸料板镶件 5、7—冲孔凸模 6—导正销 9—预冲孔凸模 11—翻孔凸模 12—模柄 13、17、28—切废料凸模 15、16—弯曲凸模 18—固定板 19—卸料板垫板 20、24、26、31、33—下模板镶件 21—导柱 22—下模弯曲镶件 23—顶杆 25—套式顶料杆 27—内导料板 29—翻孔凹模 30—限位柱 32—字印 34—小导柱 35—螺钉 36—下模座 37—垫块 38—承料板 39—外导料板
3)卸料板采用弹压卸料装置,可在冲裁前将板料压平,防止零件翘曲。
(2)关键零部件设计
1)翻孔凸模及凹模设计要点
翻孔凸模11及翻孔凹模29是工位④翻孔中的关键部件。其设计的好坏直接影响翻孔的质量,现举例说明如下(图2-48):
①平顶凸模(图2-48a)。它常用于大口径且对翻孔质量要求不高的制件。用平顶凸模翻孔时,材料不能平滑变形,因此翻孔系数m应取大些。
②抛物线形凸模(图2-48b)。其工作端有光滑圆弧过渡,翻孔时可将预冲孔逐渐地胀开,减轻开裂,比平底凸模效果好。
③无预冲孔的穿刺翻孔凸模(图2-48c)。其端部呈锥形,a取60°。凹模孔带台肩,以控制凸缘高度,同时避免直孔引起的边缘不齐。
④有导正段的凸模(图2-48d)。此凸模前端有导向段,工作时导向段先进入预冲孔内,先导正工序件的位置再翻孔。其优点是:工作平稳、翻孔四周边缘均匀对称,翻孔的位置精度较高。
⑤带有整形台肩的翻孔凸模(图2-48e)。此凸模后端设计成台肩。其工作过程是:压力机行程降到下止点时,凸模台肩对制件圆角处进行校正,以此来克服回弹,起到了整形作用。
⑥凹模入口圆角(图2-48f)。入口圆角对翻孔质量的控制至关重要。入口圆角r主要与材料厚度有关:
t≤2时r=(2~4)t
t>2时r=(1~2)t
当制件凸模圆角小于以上值时,应加整形工序。
通过对以上举例介绍及结合制件的要求,该模具翻孔凸模头部设计成图2-48b所示的抛物线凸模。
图2-48 凸模及凹模设计要点
a)平面凸模 b)抛物线凸模 c)无预冲孔的穿刺翻孔凸模 d)有导正段的凸模 e)带有整形台肩的翻孔凸模 f)凹模入口圆角