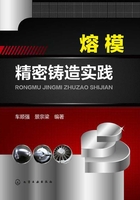
1.3 熔模铸造工艺的特点
熔模铸造工艺具有以下优点。
(1)熔模铸件的尺寸精度高,表面粗糙度小 由于熔模铸造采用尺寸精确、表面光滑的可熔性模,而获得了无分型面的整体型壳,且避免了砂型铸造中的起模、下芯、合型等工序带来的尺寸误差,熔模铸件的棱角清晰、尺寸精度可达到CT4~6级,表面粗糙度可达Ra0.8~1.25μm。所以,熔模铸造所生产的铸件已较接近于零件最终形状,可以减少铸件的加工工作量,并节省金属材料的消耗。
(2)适用于铸造结构形状复杂、精密的铸件 熔模铸造可铸造出结构形状复杂、精密,并难于用其他方法生产加工的铸件,如各类涡轮、叶轮、空心叶片、定向凝固叶片、单晶叶片等,也可以铸造壁厚为0.5mm,铸孔最小为1mm的小铸件,质量小至1g,最大至1000kg,外形尺寸可达2000mm以上的铸件,还可以将原来由许多零件组合的部件,进行整体铸造。
(3)合金材料不受限制 各种合金材料,例如碳钢、合金钢、不锈钢、高温合金、铜合金、铝合金、镁合金、钛合金、贵金属、铸铁等均可以应用熔模铸造方法生产铸件,特别是对于难以切削加工的合金材料,更适合于熔模铸造工艺。
(4)大、小批量生产均可适用 熔模铸造工艺由于普遍采用金属压型来制造熔模,故适用于大批量生产,但应用价格低廉的石膏压型、易熔合金压型或硅橡胶压型(常用于艺术品及首饰铸造)来制模,则也可以适用于小批量生产或试生产。
(5)熔模铸造工艺具有以下局限性。
①熔模铸造过程复杂、工序多,影响铸件质量的工艺因素多,所以,必须严格控制各种原材料及工艺操作,才能稳定生产。
②最适用于生产中、小铸件,能铸出最大孔径3~5mm,最大通孔径5~10mm,最大不通孔径5mm,最小铸槽≥2.5,最小槽深≤5mm。
③生产周期较长。
④铸件的冷却速度较慢,易引起铸件晶粒粗大,碳钢件还容易产生表面脱碳层。