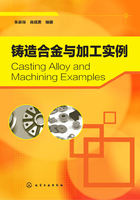
第一节 中锰球墨铸铁
最早的球墨铸铁出现在1949年,由英国皇家学院用金属铈处理铁水使石墨球状化,随后前苏联机械科学研究院用镁处理铁水制成球墨铸铁。此后,各国相继采用冲入法和压力包加镁法以纯镁作球化剂投入生产。随着进一步研究,人们采用镁铜合金和镁硅合金作球化剂,以减缓镁气沸腾。这种价格便宜而性能可与钢相媲美的材料的出现受到全世界的关注,我国也开始球墨铸铁的研发。笔者参与了我国球墨铸铁的探索试制。通过研究发现即便加镁过量或孕育不佳而铸成全白口铸铁,经900℃以上退火2h,也能变成完好无损的球状石墨。所获得的球墨铸铁的显微组织以珠光体+铁素体包围石墨球,被称为牛眼状组织。其力学性能近似45号铸钢,因而在机械工业中广泛应用,可取代中碳铸钢件。
为了适应冶金、矿山、动力机械、石化机械等行业的多样需求,在普通球墨铸铁的基础上研究发展具有特殊性能的新型球墨铸铁材质和工艺方法。笔者在钼钨合金球铁研究基础之上,开展了中锰球墨铸铁的研究。该铸铁可以在工业上很多领域替代钢材,如采矿业中大型球磨机用磨球每年消耗大量锻钢球,用中锰球铁替代锻钢将节约大量资金。此外球磨机衬板、破碎机锤头以及大型斧头(锻钢斧头不易淬透淬硬)等方面也有广泛应用。但实践中发现中锰球铁的质量与生产工艺密切相关,如某铸造厂生产的中锰球铁磨球硬度仅为HRC38,这主要是由于材质的化学成分和生产工艺不当所引起的。实质上这种硬度较低的中锰球铁的含锰量大于6%~9%,形成80%以上的奥氏体+碳化物,没有马氏体和贝氏体,或者含锰量小于4.5%,形成大量索氏体基体而性脆,从而导致极易断裂。另一种引起其质量参数较低的原因则可能是其在砂型铸造中未控制磨球的冷却过程所造成的,总之是属于低硬度、不抗磨,在使用过程中易破碎的不合格的中锰球铁产品。
根据在科研和生产实践中的总结所掌握的中锰球铁材料的产品生产技术核心有二。其一,除特大型衬板外,化学成分中含锰量必须限定在4.8%~5.8%范围内,不可达到或超过6%,也不可小于4.5%,并配合以适宜的碳硅当量。其二,既然要铸态应用,不对铸件做热处理,则仍须遵循其相变规律去控制铸件的冷却工艺。
控制铸件冷却工艺的原则是使红热铸件从1000℃(最低700℃)在空气中冷却,当铸件变黑(400~450℃)时,使铸件缓慢冷却(可堆在一起,也可放入砂坑中)。这种冷却制度最适于铁型浇铸磨球、锤头、小衬板。如果是砂型则显然劳动强度大了。浇铸大衬板时应采用半面(工作面)铁型,半面潮砂型,可以不热开箱。若用砂型生产锤头和衬板,可不须控制铸件冷却,做一次正火处理,也是可以获得良好显微组织和性能的(900℃、1~2h空冷,不回火)。通过多年的开展中锰球墨铸铁研究与生产的经验,对从科研与生产实践中取得的认识和经验工艺技术概括如下。
一、化学成分与显微组织
化学成分(其中括号内为最佳成分):碳3.2%~3.5%(3.3%),硅3.4%~3.8%(3.6%),锰4.8%~5.6%(5.2%),镁0.022%~0.025%(0.024%),磷<0.08%,硫<0.02%,稀土0.02%~0.04%。
按照上述成分制备出的铸铁的显微组织如图3-1所示,由占基体70%以上的马氏体和上、下贝氏体包围球状石墨+15%的高韧性的奥氏体包围着10%以下的碳化物,这种组合结构使材质硬而不脆,硬韧和谐,适应冲击磨损条件。

图3-1 中锰球墨铸铁显微金相图
二、铸件生产工艺
铁水的熔炼可以用冲天炉、感应炉、电弧炉或冲天炉与感应炉双连等;金属炉料可以用生铁+废钢或生铁+回炉铁+废钢为基本炉料,配以适量的锰铁和硅铁熔成原铁水,若含锰3%~7%的生铁为原料则更有利,但所采用金属原料的化学成分必须明确;待铁水全熔后,取样分析碳、锰、硅的含量,不符合要求的成分,应予调整。分析期间应用小电流保温铁水。
球化处理是制备球墨铸铁的最重要步骤:原铁水成分合格后,迅速加大电流升温到1400~1450℃,扒渣出铁。设铁水包每包盛铁水200kg,则球化剂(稀土镁合金)按0.7%(无须1.2%或1.4%)。一般球铁计算为1.4kg,事先将该合金打成ф5~10mm小粒,放入红热的包底,上面覆盖100mm厚的干燥的稻草或草袋片,冲入铁水总量的2/3,然后用铁锹向出铁槽的1/3铁水流中冲入ф5mm的干热硅铁粒,按200kg铁水的1.4%计算(约为2.8kg),进行孕育石墨化处理。用钢棒搅拌0.5~1.0min,用铁勺取样浇铸三角试片检查断口。
炉前检验石墨球化程度可采用两种方法:一种是用朱氏肉眼观球法;另一种可用三角试片,将木型的尖部向下压入潮砂型,取出木型备用。当向砂型中浇入铁水凝固后,用钳子夹出三角试片,在空气中晃动加快冷却到紫黑色时,淬入水中冷却到室温,然后打断,看断口。若三角试片尖端有≤5mm白碴,整个断口呈现出丝绒状银灰色,则显微组织合格(球化良好),如有黑点则球化不良,应用事先准备好的钢质钟罩压入铁水中0.2%的稀土镁合金,然后浇铸。如果试片断口上呈现出多个条形暗白点(为碳化物),说明硅量太少,应该用钟罩压入硅铁粒(质量分数为0.4%)进行第二次石墨化,或者向手端包中放入硅铁粉(每个手端包底上放入硅铁粉200g),冲入铁水后浇铸[以每手端包铁水质量20kg计,即加入硅铁1/100(铁水重)]。移开使空冷,全黑时集中缓冷,可大批生产磨球。
三、铸件造型和冷却工艺
通过研究中锰球铁的奥氏体转变曲线发现必须控制铸件冷却速率才能得到理想的显微组织与性能。铁水成分为C 3.5%、Mn 5.8%、Si 3.7%、S 0.02%、P 0.10%的中锰球铁冷却过程中,650~750℃最易析出珠光体,500~650℃逐次析出索氏体和屈氏体,在320℃左右转变成上、下贝氏体,在150℃开始转变成马氏体,并有一部分残留的奥氏体。一般450℃~1000铸件应快速冷却,如空冷或风冷,在450℃以下铸件应缓慢冷却(集中放入沙坑或堆放)。对于衬板、锤头类产品可经900~940℃正火,全黑后(450℃)入炉缓冷到50℃出炉,或全黑后堆集冷却。
为适应这种控制冷却的要求,最好采用铁型,凝固后即开箱,才便于控制冷却。若必须使用砂型,据笔者经验不宜用砂箱的潮砂型,也便于去砂控冷,待铸件冷却降至室温时,打掉冒口清理。此外经验表明使用成排铁型,架高500mm,型腔刷石墨涂料,铁水凝固后开箱,红球落地后移开使其空冷,待其全黑后缓冷,即可大批量生产磨球。
通过上述工艺制备出的磨球硬度HBN>480~520(低铬白口铸铁的HBN仅320~340);试片的冲击韧性αk为18~22J/cm2(低铬白口铸铁αk为2~4J/cm2),珠光体球墨铸铁的HBN180~220,αk为8~12J/cm2,可见含Mn 5.4%,按上述工艺生产的中锰球铁铸件材质,具有硬韧协同的独特性质。
四、大衬板生产工艺
以几何尺寸为730mm×390mm×150mm,单个重量>110kg的大衬板为例,根据体积大、壁厚、质量较重和使用条件的要求,来确定相应的力学性能(硬度和冲击韧性)。按所要求的性能,选择适宜的显微结构。再按照显微结构的要求,确定合理的化学成分和正确的熔铸工艺。
1.化学成分
要求衬板的工作面之表层20~25mm处,具有较高的硬度,争取达到HRC≥55,下箱宜采用铁型,厚度同衬板的1/2。其后的部位具有HRC50~45的硬度和αk≥15J/cm2的韧性。这样,该衬板在使用过程中既不会断裂又比原ZG42低合金钢衬板有较长的使用寿命。这种分层的性能需要有分层不同的显微组织。即表层(25mm内)具有碳化物(40%~50%)+针状马氏体+下贝氏体+极少的残余奥氏体组织。从表层25mm以后的部位具有马氏体+上、下贝氏体为主+10%~15%的奥氏体基体,<15%粒状碳化物。石墨为球状。化学成分宜用C±3.3%,Si±3.5%,Mn6.0%~6.5%。
2.炉前处理
铁水熔化温度1500℃,出炉温度1380℃,处理前铁水含硅量控制在3%~3.3%。浇铸温度1260~1320℃,铁水包预热温度>500℃。包底坑内放置稀土硅镁合金(Mg 7%~9%)球化剂0.7%(占包内铁水量),粒度10~20mm。球化剂上面压盖干燥的覆盖物。在冲入包容量2/3的铁水后,随其余1/3量的铁水流冲入孕育(墨化)剂(75 SiFe或SiFe+Si-Ca),质量按铁水总量的1.4%计(孕育剂应预热300℃,粒度5mm),采用适宜的覆盖剂,立即作三角试片测试。若试片断口尖部有小于5mm白口,余部呈银灰色且丝绒状茬口,说明球化良好,而且显微结构合格,即进行挡渣浇铸。壁厚小于50mm的小衬板,化学成分宜用C 3.3%~3.5%,Si 3.5%~3.8%,Mn 5.0~5.5%。采用潮砂型,无须半面铁型。抗冲击磨损球墨铸铁实际应用与有关材料对比结果如表3-1所示。可见中锰抗磨球铁在实际使用中具有更长的寿命。
表3-1 抗冲击磨损球墨铸铁实际应用与有关材料对比结果
