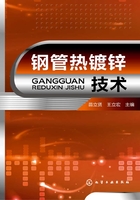
第七节 硅活性钢对热镀锌的影响
一、高硅活性钢热镀锌时的主要缺陷
一般认为,适合于热镀锌的钢是低硅量的沸腾钢,《美国金属手册》中指明要求硅含量小于0.05%。这类钢热镀锌后得到紧密、连接、均匀的金属间化合物组织。连续铸钢技术的普及,给热镀锌带来了新的问题。与传统的铸锭技术不同,连续铸钢技术要求铸钢前对钢铁进行充分脱氧,通常采用成本较低的硅作为脱氧剂,因此该技术生产的钢都是硅含量较高的镇静钢或半镇静钢。热镀锌时,钢中硅会显著增加铁与锌的反应活性,故称此类硅含钢为“活性钢”。含硅活性钢热镀锌时往往出现灰暗、超厚及黏附性差的镀层,使产品质量明显降低。因此,含硅活性钢的热镀锌问题一直备受关注。
解决含硅活性钢热镀锌的“活性”问题的途径主要有两条:一是改变热镀锌的温度;二是在热镀锌中加入微量合金元素。为此,发展了包括多元锌合金、锌镍合金、锌锰合金、锌镁合金、高温镀锌等热镀锌技术。这些技术都是通过合金元素的作用或通过改变反应温度来控制铁锌反应,以获得具有紧密而连续的层状组织、适当的锌层厚度、较好的外观质量和耐腐蚀性及黏附性的镀层。
含硅活性钢中,含有来自连续铸钢时作为脱氧剂残留下来的以及为增加钢的强度而特地加入的硅。圣德林效应表明,钢中含有一定量的硅会显著增加铁与锌的反应,其影响程度随硅含量的不同而不同,在硅含量为0.07%~0.1%及0.3%以上出现反应峰值,表现为热镀锌层活性及生长速率明显增加。
1.硅含量对铁锌金属间化合物相层生长速度的影响
含硅活性钢热镀锌时,铁锌金属间化合物相层的结构、厚度和形成过程主要取决于硅在钢中的存在与否。在硅的影响下,钢基体与锌的反应受最初的溶解过程控制,其镀层生长随时间呈直线规律。当含硅钢表面形成硅的氧化物时,反应受铁锌金属间化合物相层中的扩散控制,其镀层生长呈拋物线规律。
钢中硅含量对金属间化合物层生长速率(厚度变化)的影响与热镀时间、浸镀温度有关。硅含量WSi小于0.4%的钢在短时间(≤20s)浸镀时,金属间化合物相层的生长速率并不随硅含量的增加而增大,当浸镀时间达到2min时,相层生长速率才转而增大;对于硅含量大于0.4%的钢,短时间的浸锌会使生长速率随硅含量增加而增大。该现象还与热度温度有关,较高的浸锌温度使生长速率变化更明显。上述结果说明,钢中的硅对金属间化合物相层生长的影响,在短的浸镀时间里不起作用,只有经过一定时间的浸镀反应,硅在相层生长行为中才发挥作用。
2.硅对影响铁-锌金属间化合物反应形式
钢中硅元素在热镀锌时影响铁锌金属间化合物层的生长,主要表现在影响铁和锌的扩散。由于硅原子与铁原子的亲和力大于硅和锌,硅原子溶进铁里,形成Fe-Si化合物。Fe-Si首先以极细小的、分离的形式存在,作为惰性物质迁移,通过仍是很薄的金属间化合物相层,到达熔融锌界面。这些Fe-Si粒子如果足够细小,且在ξ层相接口熔融锌处有足够的过饱和度,将促进熔融锌中ξ相的形核,形成破碎的相层。当Fe-Si粒子超过临界尺度时,其作用降低,反应不再发生,将形成紧密的铁锌金属间化合物相层。
二、硅对镀锌层影响的特征
1.力学性能差
众所周知,含硅钢的批量热镀锌,在WSi接近0.1%(即圣德林峰处)或大于0.3%时,会导致非正常的或活性的镀层形成。在含硅热轧钢的表面,活性区通常随机分布。对这些钢进行热镀锌时,在镀层中会形成粗大的ξ相晶粒和厚的Γ相层,使镀层外观和力学性能变差、锌耗增加。
局部迸发式生长是热轧状态活性钢热镀锌的典型特征。当表面通过机械的或化学的方法处理后,活性镀层的形成会形成显著增强。在表面状况和冷加工对含硅钢热镀锌反应的影响方面已进行过大量的研究,但未提出完全一致的机制来解释局部活性镀层组织形成的原因。这里面,其他的因素,如第三元素含量、晶粒位元向和表面或亚表面氧化,都可能对活性现象起到某种作用。在热镀锌过程中,尽管锌浴温度、镀锌时间等参数一定,但由于镀件在镀锌前的加工过程中可能引起上述因素的变化,使镀层组织有很大差别。因此,正确区分含硅钢表面的各种因素对热镀锌的影响,将有助于了解含硅活性钢热镀锌的问题。
2.亚表面氧化
活性钢中硅的存在时活性镀层形成的重要原因。许多研究都给出了基本相同的规律:钢中WSi约为0.1%时,镀层活性增加,反应速率出现峰值;在WSi接近0.2%时,活性减小;WSi高于0.3%时,反应速率又明细增加。然而,含硅钢的活性与钢表面固溶硅含量有关。研究表明,钢表面的硅以Fe-Si固熔体形式存在,将会增加热镀锌活性,而硅以SiO2形式存在时,将不会增加活性。因此,在活性钢热镀锌时,应考虑钢表面的固溶硅含量。
含硅钢的热轧加工过程会导致钢材亚表面氧化层的形成,该亚表面氧化层中硅的氧化物以小颗粒的形式存在于晶界和晶内。由于硅的氧化物的形成能大于铁的氧化物的形成能,固溶的硅将会优先与氧发生反应形成一种稳定的非活性化合物,并存在于亚表面晶界和晶内。因此,对活性镀层行为的抑制与这些惰性的硅的氧化物在亚表面氧化层的沉淀有关。K.Nishmura等对不同含硅量的钢板于高温酸洗及抛光后,在不同条件下进行预热处理,发现含硅钢在预热处理过程中,在表面形成氧化膜的速度大于不含硅的钢,同时液体锌与钢基体之间的反应受到了限制。对钢基体的分析表明,在钢基体表面出现了硅的聚集区,并认为该聚集区是在预热处理工程中出现的,对随后的热镀锌反应活性有抑制作用。
V.Leroy等指出热轧钢在接近表面的亚表面氧化层硅含量有显著的增长。经离子探针(IMA)分析,钢基体整体硅含量WSi只有0.228%的表面,硅的富集WSi高达8%,而WSi仅为0.01%的钢,表面硅富集WSi超过1%。钢在不同深度上的元素分布测定证实了,氧含量的降低与硅含量的变化相符合。对WSi为0.01%钢,除了表面,在所有深度上都未探测到硅。在WSi为0.228%的钢中,硅在所有深度都有明显分布,这可能是钢中固溶态的硅。这两种钢在去除亚表面氧化层的酸洗及热镀后表现出显著的差别。低硅钢形成了典型的紧密机构镀层,而高硅钢形成的是活性镀层,表面固溶态的硅足以使镀层不稳定。
含硅活性钢在热镀锌时,须考虑与锌反应的钢基体表面的固溶硅含量。热轧含硅钢表面固溶硅含量受作用相反的两方面的影响:一方面由于高温加热时亚表面氧化,使部分硅形成氧化物,降低了固溶硅含量;另一方面,镀前钢材的锈蚀和镀前酸洗等对钢亚表面氧化层的腐蚀,使钢基体表面固溶硅含量不同程度增加。因此,腐蚀程度也导致镀层组织结构的变化。图2-22为高硅含量钢亚表面氧化层的腐蚀深度对镀层组织的影响。从图中可以看出,随着腐蚀深度的增加,镀层厚度明显增加,镀层结构也由层状变为分散状结构。由此可知,对于含硅活性钢镀件,延长酸洗时间、酸洗-返镀、镀前喷砂处理等都会因亚表面氧化层的破坏而改变表面固溶硅含量,导致镀层活性增加。

图2-22 高硅含量钢亚表面氧化层的腐蚀深度对镀层组织的影响(由上至下腐蚀深度增加)
氧在亚表面氧化中起着重要的作用。为了证实氧在反应中的重要性,G.Hansel对4种不同活性的钢(WSi为0.023%~0.06%)进行了热镀锌。低硅含量钢经几次酸洗-返镀后才具有活性。当置于氧化气氛(N2-O2-H2O)中退火后,均变为非活性,而高硅含量的钢需要更高O2量的氧化气氛或更长的加热时间来达到同样效果。但是,当在非氧化气氛(H2)中进行退火时,镀层形貌没有出现改变。该结果表明,含硅钢通过亚表面氧化抑制活性时,与预热处理气氛中O2含量和加热时间有关。
3.表面粗糙度
表面粗糙度对热镀锌层的形成有明细的影响。钢基体表面的凹凸会使铁锌合金层的生长形态发生变化。图2-23描述了热镀锌层在不含硅钢的不规则表面上的生长特点。在凸起处,刚形成的ξ晶体相分离,使液态锌可穿透到ξ/δ界面附近,支持ζ相连续快速生长而形成迸发状晶粒。在凹入区域,由于生长受扩散控制,可得到紧密稳定的结构。

图2-23 钢材凹凸表面的热镀锌层生长形态
在粗糙表面的凹入点形成稳定结构,可能是由于体积收缩的结果,产生足够的压应力使铁锌合金相层稳定。稳定层一旦形成,无论产生稳定性的原因是否存在,稳定性都会保持下来。此外,在表面凹陷处具有支持富铁层形成的条件。由于提供了大面积的表面供体积收缩的合金层生长,使反应所需的铁供应充足,而同时锌的供应却由于锌难以进入凹陷处而减少。在这些位置,经常发现厚的Γ层。
F.Petter等研究了钢材含硅量、表面粗糙度的综合影响。将不同含硅量的钢板分别用粗金刚砂、细金刚砂、玻璃微珠进行喷砂处理,以及用酸洗的方法进行处理,得到了从粗到细不同的表面粗糙度。图2-24为不同表面粗糙度钢材含硅量与热镀锌层厚度的关系。试验结果表明,用粗金刚砂处理的钢在不同的硅含量范围都生成了厚镀层,这种表面相对较粗糙的钢在凸起处生成了迸发状ξ相结构,而在凹入处形成紧密结构。而经酸洗和玻璃微珠处理的钢在硅含量WSi为0.08%~0.12%时形成典型的须状结构。细金刚砂处理WSi为0.08%的钢时,镀层厚度降低,形成了紧密的连续ξ层和平坦的ξ/δ界面,但处理WSi为0.12%的钢时,镀层厚度却急剧增加。这是因为在WSi为0.08%的钢中,镀层稳定的机制是富铁层的形成,当硅含量WSi增加到0.12%时,不再形成稳定的Γ层。这种转变可能是在生成稳定富铁层时,系统随硅含量的少量增加而失稳的结果。

图2-24 不同表面粗糙度钢材含硅量与热镀锌层厚度的关系
上述结果表明,细金刚砂与玻璃微珠处理的钢表面粗糙度虽然相近,但是由于形貌不同,最终得到的镀层的稳定性差别很大。因此,不能简单地将表面粗糙度用于评价是否产生活性镀层结构的参数。